What makes flexible packaging such a positive choice? Better performance and product innovation, of course. Industrial packaging has a longstanding relationship with bulky, heavy containers. Perhaps it is difficult to imagine how thin materials can stack up against them. In many cases, the art and science behind lightweight films enables them to outperform their bulkier predecessors.
Flexible, industrial packaging provides workable, dependable solutions for longstanding problems in a cost effective way and with low environmental impact. They’re capturing more and more of the market share, and here’s why.
Forward-Thinking Product Design and Development
Innovation is at the heart of flexible packaging design and development. The goal isn’t just to offer a different packaging option but to create something that performs better on multiple fronts.
Packaging can be a key element in product safety and end-user convenience while fitting into your company’s environmentally-aware policies. How is that possible? The Flexible Packaging Association (FPA) offers a few facts:
- Flexible packaging isn’t one thing; it’s many things. Product shelf life is extended and waste is reduced by choosing a film with the correct attributes.
- It contains more product using fewer resources, which reduces warehouse space and transportation costs.
- A metal container of comparable size uses 75 percent more energy to manufacture and creates significantly more CO2 emissions.
It can guard against solvent breakdown or product spoilage in a durable material that allows for product agitation and dispensing, all in one environmentally-sound unit. That’s much more than just a container.
Liner Films Address Various Industry Issues
Advancements in film technology make flexible packaging a viable option for industries that might not have considered it before. For example, general-use, low-density polyethylene drum liners combine high tensile strength and elongation with tear and crack resistance. Ultrasonic and heat sealing seam technology supports the integrity and overall performance of the liner.
Anti-stat liners employ an internal anti-static agent to reduce static buildup and dry static cling, which protects flammable materials from accidental ignition. Where high oxygen and water vapor barrier concerns exist, round bottom foil liners provide a form fitting liner with a foil inner layer for high barrier protection and multiple options for product contact surfaces include low density polyethylene, polypropylene, or polyester.
These IBC liner options are FDA compliant:
- Ethylene vinyl alcohol (EVOH): strong, flexible, transparent and widely-used in the food packaging industry.
- Flexus™ and Flexus HF metallocene LLDPE: flexible, durable and crack-resistant for general use
- Tenalon™: abrasion-resistant, strong, durable, co-extruded nylon
Flexible materials are unparalleled in their ability to achieve more with less. They're overtaking traditional packaging materials on so many different levels that they’re steadily moving toward becoming standard. The FPA says flexible is the “second largest packaging segment in the U.S.”
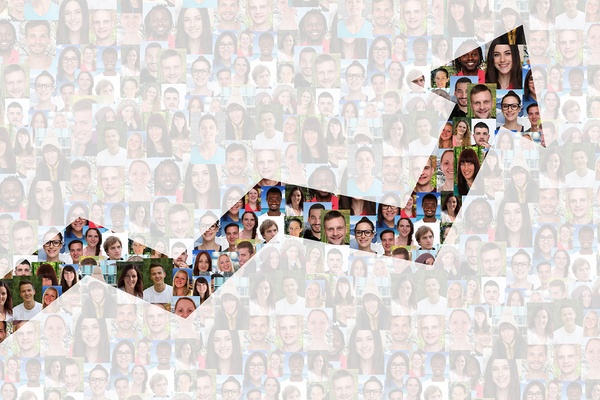
End-User Factors Shape Today’s Performance and Tomorrow’s Innovation
When sourcing a new, flexible packaging option, the more the manufacturer knows about your needs, the better. Details about the product, in-house manufacturing, and handling processes, as well as site condition factors, help build a comprehensive profile.
This information helps pair you with the right product. If your needs vary, modification and customization, such as special venting or a different fitment location, is often an option. Looking ahead, your information does something more; it helps define the future of flexible packaging.
You might be asked about these and other specifics:
- Product bulk
- Whether the product is hazardous
- Which market the product is designed for
- Product particle size
- Product special characteristics
- Liner or bag type (drum liner, IBC liner, etc.)
- Liner film, if known
- Fill method
- Characteristics of the work area
- Discharge preference
- Ideal discharge rate
- Handling, racking, and transportation methods
- Regulatory compliance concerns
With these and other details, the manufacturer can provide the best flexible packaging solution today and create a cycle of ever-improving design and technology in the future.
Flexible Packaging Supports Regulatory Compliance
Regulatory compliance issues can be a significant barrier between using familiar packaging materials and switching to an unknown material. However, flexible packaging has a strong reputation as a safe, protective, resilient packaging choice that supports compliance.
Depending on the end-use, flexible packaging in the U.S. must remain compliant with voluminous federal regulations, according to the FPA.
Some regulations include:
- Food, Drug & Cosmetics Act (FD&C)
- Toxic Substances Control Act (TSCA)
- Consumer Product Safety Act (CPSA)
- Consumer Product Safety Improvement Act (CPSIA)
- Federal Hazardous Substances Act (FHSA)
If UN certification is an issue, certain flexible packaging meets UN requirements for containing and transporting hazardous materials that require Class II and III packaging. To qualify, packaging must pass rigorous third-party testing that reproduces the stress and strain of transportation.
Flexible materials also support Current Good Manufacturing Practice (CGMP) regulations, the standard for food and pharmaceuticals, and helps facilitate SQF certification.
Decades ago, who could have predicted that film liners and bag-in-box containers could not only compete with, but perform better than, old standards. Food, pharmaceutical, cosmetic, chemical, and many other industries have navigated toward a future with flexible packaging.
If you're ready to learn more about how something new can yield high rewards, we're here to help. Download our food packaging product and pricing brochure to get started.