When food must be pure, aseptic packaging helps make it so. Whether you manufacture baby food or beverages, the packaging that you rely on can either support sterility and purity, or it can become a hurdle to overcome. Flexible film packaging is in the former category.
If you want to save costs and improve quality by moving away from retort packaging or you need any solution that is better than what you use now, here is what you need to know.
What is Aseptic Packaging?
When food must be sterile, so must the food packaging. Aseptic food packaging is sterile so the pure, sterilized food has the greatest chance of staying that way through every link in the chain.
Typically, aseptic food processing involves a sterilization, either through quick, ultra-high temperatures or sometimes through ultraviolet light, and a sterile environment using sterilized equipment. Sterile food packaging is filled with the sterilized food and sealed to protect it from contamination.
In some cases, food and packaging are sterilized together. This is called retort packaging, which is similar to a food canning process. Packing is filled and sealed, then the sealed unit is heated to kill any bacteria that may be present. This can be an expensive approach.
Aseptic packaging is sterile before it is filled with sterilized food. Unlike retort packaging, aseptic packaging usually does not require further sterilization after it is filled and sealed. The inspection process should be filed with the FDA and meet FDA standards for sterility of the product, sterile zones in the manufacturing process, the packaging system, and the materials used in aseptic packaging.
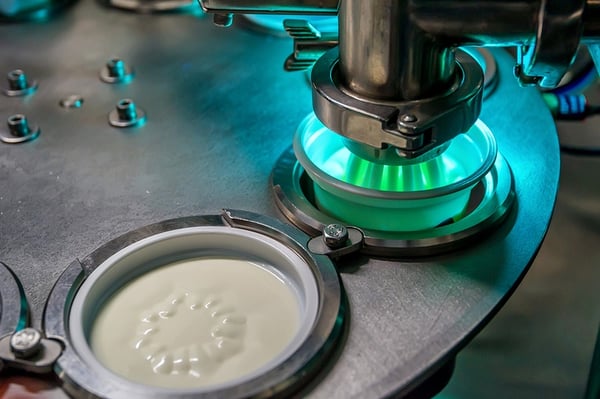
What Is Happening in Aseptic Packaging Today?
Food manufacturers now have a few choices for aseptic food packaging. According to the University of Guelph, these are the primary types of sterile food containers widely available today.
- Fill-and-seal: pre-made containers that are sterilized, then filled and sealed
- Form, fill and seal: flexible film materials that are sterilized, formed into the packaging shape needed, then filled and sealed
- Erect, fill and seal: cartons that are built, sterilized, filled, and sealed
- Thermoform, fill and seal: flexible film materials that are sterilized, thermoformed in a sterile environment, filled, then sealed
- Blow mold, fill and seal: a wide range of possible materials, such as bag-in-box and laminated plastics, that are sterilized, filled, and sealed
Advances in aseptic packaging speed, scalability, strength of materials used, resistance to contamination and effective sealing technology make flexible materials an increasingly better choice for food manufacturers.
Where Can You Find the Aseptic Packaging Solutions You Need?
Flexible film materials and aseptic food packaging processes go hand in hand. With ever-improving technology in barrier films and lighter, high-capacity options, costs go down while quality goes up.
Take the IBC Pillow-Shaped Liner, for example. IBC tote liners are shaped like a pillow and use multiple layers of low-density polyethylene (LLDPE). With the addition of a barrier film, they are ideal for aseptic applications.
IBC liner production is closely monitored using sophisticated equipment. During production, if any issue arises, such as a detected faulty seal, the entire production line comes to a halt. That prevents faulty seals from making their way into your packaging.
When food sterility matters, aseptic food packaging helps you meet your goals. It is flexible, both in a literal and a figurative sense, and it helps reduce costs by as much as 40 percent, depending on what you use now.
If you are ready to learn more, we are ready to help. Contact us for a free sample and download our corporate brochure today.