Who would have imagined 30 years ago that thin, lightweight packaging could give so many other materials a run for their money? Flexible packaging is the fastest growing segment in the market, and for good reason.
Flexible materials are not one thing, but many different things that can safely contain a wide range of products. More than just a pouch or a bag, they offer numerous container possibilities. From beverages and fresh foods to sauces and dry goods, there is probably a flexible film that can handle your job better than its closest competitor.
Here is how to fine-tune the right selection for your application.
From How Many Different Types of Film Can You Choose?
Flexible film packaging is plastic broadly, but with lots of variations. For example, polyethylene (PE) is one of the most versatile, popular, and widely-used flexible films. Polypropylene (PP) is another, and polyethylene terephthalate (PET) is another common material. Some packaging uses foil laminates and others combine semi-rigid plastics with flexible films for a custom container.
These are some of the numerous flexible packaging options available:
- Low-density polyethylene
- Linear low-density polyethylene
- High-barrier foil
- Oriented nylon
- Co-extruded nylon/EVOH
Each film has inherent properties and performs better in some applications than in others. Your choice of film or film combinations lets you fine-tune the material to the product and supply chain. Whether you need top-lidding films, pail liners or bag-in-box solutions, there’s probably a flexible film that can work for you.
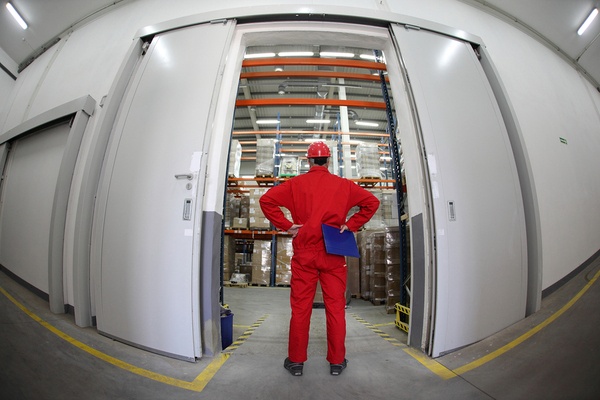
What Does Each Link in Your Supply Chain Need?
Does your product require sterilization? Does it need support for enhanced shelf life? Is there significant transportation time involved? What are the storage limitations at each level? Can you, or should you, invest in new filling equipment? The flexible film liner you choose must answer these questions and many others, as packaging is a much broader topic than just containing a product.
Switching to flexible packaging affects storage and transportation. While transportation costs are typically lower, stacking and storage must be considered if the materials vary greatly from your existing packaging.
These are just a few issues to think about when selecting your next flexible film packaging:
- Cost effectiveness, including hidden costs such as new filling equipment, at all levels of the supply chain
- Green initiatives at every level
- Enhancing product shelf life through barrier films and tamper resistance
- Reducing product waste with better filling, dispensing, opening, and resealing options
How Quickly Can Your Choice Go from Concept to Production?
Perhaps one of the most flexible aspects of flexible film packaging is its ability to quickly adapt to your needs. Switching from one glass or aluminum container to another requires significant planning and ample lead time. The effects of the change ripple out to every link in the supply chain, all the way to the end user. Switching to a new flexible film liner is much quicker and often results in lower costs.
Some flexible materials are produced quickly and lend themselves to customization virtually on the line. For example, one film may cut to numerous different dimensions, depending on what you need, and ship without any significant production delay. With rigid materials, you would encounter a whole new design and fabrication process that requires weeks or months to fulfill.
Flexible films are changing the way that the world approaches packaging. Comparatively thin, lightweight, strong, and versatile plastics can create protective bin liners, bag-in-box systems, and a host of solutions for your food manufacturing business.
At CDF Corporation, we offer numerous choices in films and protective barriers that help keep costs low, improve product freshness, and support the efforts of production, transportation, storage, and, ultimately, the end user. Contact us for a free sample and download our corporate brochure today.