The 2016 State of the Flexible Packaging Industry report showed continued, steady growth, making flexible packaging one of the fastest growing segments available in America. The Flexible Packaging Association says flexible materials grew at a rate of about 2.2 percent for $31 billion in sales that year.
Why should that matter to you? Because in the U.S. and around the world, flexible materials are not just growing in popularity, they are becoming one of the most technologically advanced options you can buy.
Chances are, you have at least considered whether or not you should transition from rigid or semi-rigid containers to flexible options. Before you make the switch, here are a few factors to ponder.
Is There a Flexible Solution for Your Product?
Perhaps the most important factor in deciding whether or not to switch to flexible packaging is whether it will work for you. If the product that you manufacture cannot be safely, easily, and affordably contained, the discussion is probably over.
Fortunately, there is an enormous array of flexible packaging solutions for everything from fresh foods to hazardous materials.
- IBC liners use multiple layers.
- Metallized polyester creates a safe water vapor and oxygen barrier.
- LLDPE films offer crack resistance and durability in a general purpose film.
- Co-extruded nylon is strong and guards against abrasion damage.
- UN-certified materials protect the product and the environment.
Through laminating technology, you are not limited to one film only. Combining films lets you customize to meet the needs of the product, the filling machinery, handling practices, environmental factors, storage limitations, and end-user preferences.
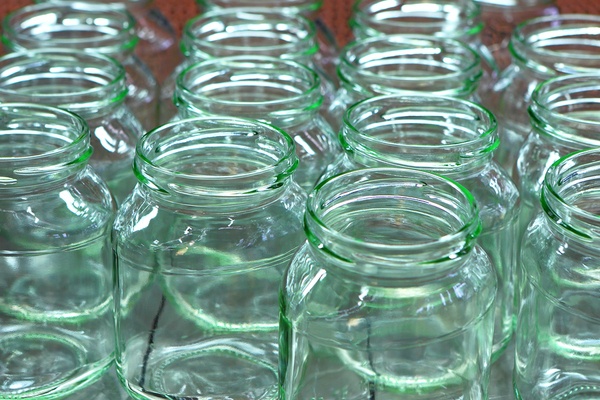
Can Your Supply Chain Handle a New Packaging Material?
Switching to flexible materials affects not just your business but everyone else’s in the supply chain from the transportation company to the end user. If you switch packing to flexible materials, are your supply chain partners equipped to handle the change?
Flexible packaging is usually easier to handle, not more difficult. It is less prone to breakage and it is much more lightweight than glass, metal, or rigid plastics. Because flexible materials hold more with less, the same product volume takes up less space. There are fewer transportation vehicles needed and less space in storage.
Flexible packaging also helps keep costs down for everyone involved. In fact, cost reduction is one of the most attractive and universal benefits. Packaging Strategies reports that over time, the smaller, lighter qualities could translate to big savings in fuel costs, handling, storage, and product loss.
What are Your Green Manufacturing Goals?
Does your business have green goals? Many companies do, but there is a point where you might hit a wall. Rigid containers can only offer so much toward lowering your carbon footprint. Flexible materials are designed for it.
Unfortunately, when some people think “flexible,” they think “plastics that do not degrade.” It is time to put that notion to bed. Flexible materials are incredibly green and Earth-friendly. Here are just a few of the numerous reasons why:
- Fewer raw materials
- Significantly less packaging waste
- Smaller dimensions
- Fewer transportation vehicles
- Lower fuel consumption
- Fewer carbon emissions
- Smaller storage areas with less reliance on fossil fuels for conditioning
- Longer shelf life at room temperature
- Recyclability (in some, but not all, cases)
If there is room to improve your green manufacturing practices, flexible packaging might be the answer for which you are looking.
No matter what product you manufacture, freshness is vital. Dry goods go stale, fresh foods spoil, and food-borne illnesses put everyone at risk. For foods, better freshness protection by way of improved packaging means less food waste and a lower risk of people getting sick.
One of the most relevant examples today is fresh food and water delivery to people who are desperate for it, such as those who have survived a natural disaster and people living in poverty-stricken areas. Some films also go from refrigeration to heat for cooking without the need for a skillet, pot, or utensils.
Flexible materials offer a longer shelf life, protection against contamination, UV resistance, and many other benefits under extreme conditions. Imagine how they can perform for you.
If you are committed to rigid packaging because it is familiar, think of the humble butter wrapper. It is flexible and it has been around for generations. Flexible materials have expanded beyond the feed sacks and sugar bags of 100 years ago because they work and showed great potential. Food manufacturers around the world are moving toward flexible film packaging now because it works better.
If you are on the verge of making the switch from rigid containers to flexible packaging, we can help. Download our Bag-In-Box brochure for more information.